The challenge
As Lagor Srl scaled up its transformer core production, the internal logistics system reached its limits. With cores weighing up to 200 tons, traditional transport options—like overhead cranes or rails—lacked the flexibility to navigate the evolving factory layout.
Outdoor assembly became increasingly impractical due to rust risk: just a few minutes of unexpected rain could delay entire projects. Cranes worked for small components, but not for massive units. The team needed a solution that could scale with core sizes, reduce weather dependency, and operate safely without a complete redesign of their facility.
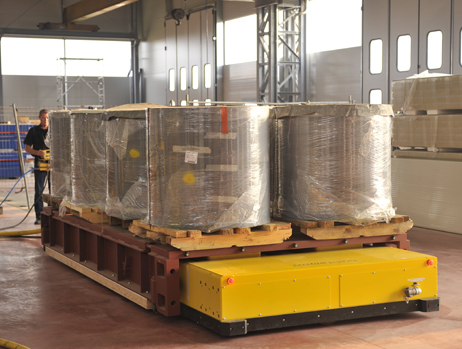